Phone: +55 (19) 3535-6550
E-mail: sulplast@sulplast.com.br
Av. Sulplast, 1969 - Distrito Industrial - Rio Claro/SP - Brazil - 13505-680 - Webmail
Technologies and processes
Sheet extrusion
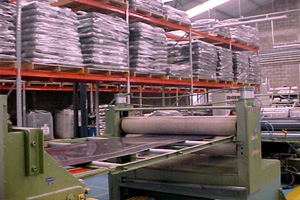
Our factory counts on extruders capable of transforming into sheets, various types of polymers such as ABS (acrylonitrile butadiene styrene), PP (polypropylene), PPT (polypropylene with mineral filler), PSAI (high impact polystyrene), PE (polyethylene), Noryl, among others.
In this plastic transformation process, the filler of the extruder is fed with granulated material and taken by gravity to the threads of the equipment, where the processes of compression and thermal fusion begins. By rotational action, the material is transported through the heated zones of the cylinder, which proceed according to the temperature gradient until the polymer reaches the matrix, where the molding will be carried out in the pre-established form. Subsequently, in an automated way, the cut is made according to the measures defined for the final product of the Extrusion.
As Sulplast's Vacuum Forming production is mostly supplied by internally extruded sheets, we consider this aspect a great competitive differential of the company, since it allows Sulplast to control all factors involved in sheets production, in addition to ensuring more flexibility to attend to volume increases and customer reprogramming.
Moreover, we have the know-how to coextrude vinyl, fabrics and various other special materials. Widely used in the manufacture of internal vehicle coatings. This production system allows versatility and a differentiated quality finishing to the products.
Furthermore, Sulplast has strategic partners capable of manufacturing HDPE sheets from co-extrusion: high impact polystyrene with acrylic co-extrusion (PSAI + PMMA), acrylonitrile butadiene styrene with acrylic co-extrusion (ABS + PMMA), among others.